The Food Manufacturing Skills Crisis: Bridging the Gap Between Industry 4.0 and Traditional Production Teams
The UK's food manufacturing sector stands at a critical crossroads. With advanced automation technologies revolutionising production processes, a significant disconnect has emerged between the sophisticated capabilities of Industry 4.0 systems and the skills of the existing workforce. This gap isn't just a minor operational challenge—it represents an existential threat to the sector's competitiveness, productivity, and long-term sustainability.
The Scale of the Skills Crisis in UK Food Manufacturing
The UK food and drink manufacturing sector, the country's largest manufacturing sector, contributes £38 billion in Gross Value Added to the economy and employs approximately 500,000 people across 12,500 businesses, according to the Food & Drink Federation (FDF). However, this vital industry faces a perfect storm of challenges threatening its workforce capabilities.
Chronic Skills Shortages
Recent data from the Food and Drink Federation reveals that the number of vacancies per 100 employees increased to 9.1 in Q3 2022, from 6.3 in Q2 2022, with 76% of respondents reporting vacancy rates of 0–10%. The Sterling Choice, a specialist recruitment agency for the food manufacturing industry, reports that over half (56%) of companies in the food and drink manufacturing sector are facing "chronic shortages" of labour for lower-skilled roles, while 67% are facing shortages in seasonal labour.
Talent Pool Challenges
The manufacturing workforce has been decreasing steadily. According to research cited by The Manufacturer, between 1997 and 2018, the UK manufacturing workforce decreased from 4.3 million to 2.9 million. This shrinking talent pool coincides with increasing technological demands, creating a widening skills gap.
The Automation Imperative
While automation offers a potential solution to labour shortages, it creates its own skills challenges. According to a recent survey by Automate UK, more than 81% of end users said that automation was their main challenge in 2023, with three main factors driving their frustrations:
- The challenge of automating bespoke products
- The level of skilled labour needed to support automation
- The difficulty in keeping abreast of technology developments
This presents a paradox: the very technologies that could help address labour shortages require skilled workers that are in short supply.
The Industry 4.0 Revolution in Food Manufacturing
Industry 4.0 technologies are transforming food production in ways that demand entirely new skill sets from workers.
Key Technologies Reshaping the Sector
Advanced Robotics and Automation
Collaborative robots (cobots) and advanced automation systems are increasingly handling tasks that were previously performed manually, from ingredient handling to packaging. The OAL Group, a leading UK food automation specialist, showcases robotics solutions like their APRIL system that can dose over 500,000 powder additions annually from over 100 raw materials with an accuracy level of +/- 1%.
Internet of Things (IoT) and Data Analytics
Connected sensors throughout production lines generate vast amounts of data that can be analysed to optimise processes, predict maintenance needs, and ensure quality control. However, according to Food Engineering magazine, only 23% of food and beverage companies report being "extremely familiar" with smart manufacturing concepts, compared to 48% of home and personal care leaders.
Artificial Intelligence and Machine Learning
AI-powered systems can now make real-time adjustments to production parameters, identify quality issues through vision systems, and manage complex supply chain logistics. This level of sophistication requires workers who can interpret AI outputs and make appropriate interventions.
The Skills Disconnect
The implementation of these advanced technologies creates a fundamental mismatch between available skills and industry needs:
- Technical expertise gap: Traditional food manufacturing workers often lack the digital literacy needed to operate and maintain sophisticated automation systems.
- Data interpretation challenges: While systems generate valuable data, many facilities lack workers who can analyse this information and translate it into operational improvements.
- Maintenance capabilities: Advanced robotics and automation require specialised maintenance skills that are in short supply within traditional production teams.
Food Engineering magazine reports that the main barriers to digital transformation in food processing are costs (44%), knowledge gaps (41%), and skill deficiencies (39%). This indicates that even when companies invest in new technologies, they often struggle to implement them effectively due to workforce limitations.
The Business Impact of the Skills Gap
The disconnect between automation capabilities and workforce skills creates significant business consequences for food manufacturers:
Underutilised Technology Investments
Many companies invest in advanced systems that end up underutilised due to skills shortages. Automate UK's survey found that many manufacturers think too big with their automation projects, resulting in systems that teams cannot fully leverage.
Productivity Struggles
While the productivity of the UK food manufacturing sector increased slightly between 2009 and 2021, with a compound annual growth rate of just 0.8%, the benefits of automation are not being fully realised due to skills limitations.
Investment Hesitation
According to the Food & Drink Federation's State of the Industry Report, food and drink manufacturing investment has fallen by 30% since 2019, compared with other areas of manufacturing which saw investment grow by 5%. This investment reluctance is partly attributed to uncertainty about the workforce's ability to adapt to new technologies.
Innovation Constraints
Without teams that can effectively implement and optimise advanced technologies, food manufacturers struggle to innovate and remain competitive in increasingly challenging markets.
Actionable Strategies for Bridging the Skills Gap
Addressing the skills crisis requires a multi-faceted approach that combines targeted training, organisational restructuring, and innovative talent acquisition strategies.
1. Upskilling Existing Employees
The most immediate opportunity lies in developing the capabilities of current employees who already understand food production processes but need additional technical skills.
Structured Technical Training Programs
Develop comprehensive training programs focused on digital literacy, automation operation, and basic data analysis. These programs should be practical and directly applicable to daily work.
Implementation Example: One UK food manufacturer developed a three-tiered technical training program:
- Level 1: Basic digital skills and automation awareness
- Level 2: Specific system operation and troubleshooting
- Level 3: Advanced data analysis and system optimisation
This approach allowed the company to progressively build capabilities while maintaining production efficiency.
Cross-Functional Learning Teams
Create mixed-skill learning teams that pair technically proficient workers with those who have extensive food production knowledge, enabling knowledge transfer in both directions.
Implementation Example: A leading bakery business established "Tech Buddy" teams that paired younger, tech-savvy employees with experienced production workers. This not only accelerated skills development but also improved retention of institutional knowledge.
Modular Micro-Learning Approaches
Break down complex technical concepts into bite-sized learning modules that can be completed during production downtime or scheduled learning periods.
Implementation Example: A dairy processor implemented 15-minute daily "tech bytes" sessions focused on specific automation features. This incremental approach made learning more accessible and less intimidating for traditional production workers.
2. Restructuring Teams for Industry 4.0
The nature of work in modern food manufacturing requires new team structures that better align with technological capabilities.
Integrated Production Technology Teams
Create specialised teams that blend production expertise with technical capabilities, responsible for optimising the interface between human workers and automated systems.
Implementation Example: A prepared meals manufacturer established "Production Technology Specialists" who serve as the bridge between traditional line workers and the IT department. These specialists have dual expertise in food production and automation technologies.
Tiered Skill Structure
Develop clear career pathways that allow workers to progressively build technical capabilities while maintaining food manufacturing expertise.
Implementation Example: A confectionery producer implemented a five-level career framework that allows production workers to advance from basic operations to system optimisation roles through structured skills development.
Agile Work Teams
Replace rigid departmental structures with flexible teams organised around value streams or product families, with varying technical capabilities integrated into each team.
Implementation Example: Rather than maintaining separate production and maintenance departments, a ready-meals manufacturer created cross-functional teams responsible for specific product lines, with technical skills distributed across each team.
3. Attracting Tech-Savvy Talent to Food Manufacturing
Addressing the skills gap requires bringing new talent into the sector with the technical capabilities needed for Industry 4.0.
Rebranding Food Manufacturing Careers
Combat outdated perceptions of food manufacturing as low-tech or unappealing by showcasing the sophisticated technologies and challenging problems the industry addresses.
Implementation Example: The UK Food and Drink Federation (FDF) and the National Skills Academy for Food & Drink (NSAFD) launched their new 'Food and Drink Careers Passport' to make it easier for manufacturers to recruit employees for entry-level roles with accreditations in key skills.
Educational Partnerships for Pipeline Development
Establish relationships with technical schools, colleges, and universities to create specialised programs that combine food science with automation and data analytics skills.
Implementation Example: A major food manufacturer partnered with a local university to develop a "Food Technology Engineering" certificate program that provides students with both food safety knowledge and automation expertise.
Targeted Recruitment from Adjacent Industries
Actively recruit from industries with transferable technical skills, such as pharmaceutical manufacturing, automotive, or general manufacturing, highlighting the stability and innovation in food production.
Implementation Example: A UK-based meat processor successfully recruited automation specialists from the automotive industry by emphasising the sophisticated robotic systems used in modern meat processing and the stability of food sector demand.
Implementation Roadmap: A Phased Approach
Successfully bridging the skills gap requires a structured, phased approach rather than attempting to transform overnight.
Phase 1: Skills Assessment and Strategic Planning (Months 1-3)
- Conduct a comprehensive skills audit to identify specific gaps
- Develop a detailed workforce development strategy aligned with automation goals
- Create baseline metrics to measure progress
Phase 2: Initial Skills Development and Team Restructuring (Months 4-9)
- Launch training programs for high-priority skill gaps
- Begin implementing new team structures in pilot areas
- Establish mentoring programs to accelerate knowledge transfer
Phase 3: Scaling and Refinement (Months 10-18)
- Expand successful training approaches across the organisation
- Complete team restructuring
- Implement recruitment strategies for critical skill gaps that cannot be filled internally
Phase 4: Continuous Learning Culture (Month 19 onward)
- Establish ongoing learning mechanisms to keep pace with technological evolution
- Create knowledge management systems to capture and share insights
- Develop advanced career pathways that blend technical and food manufacturing expertise
Measuring Success: Key Performance Indicators
To ensure that skills development efforts are delivering results, establish clear metrics:
Productivity and Efficiency Metrics
- Overall Equipment Effectiveness (OEE) improvements
- Reduction in downtime due to technical issues
- Increase in output per employee
Skills Development Metrics
- Number of employees completing technical training programs
- Percentage of workforce with specified digital competencies
- Internal promotion rates into technical roles
Organisational Health Metrics
- Reduction in vacancy rates for technical positions
- Employee retention rates
- Internal surveys on technology adoption and comfort
Conclusion: Creating a Future-Ready Food Manufacturing Workforce
The gap between Industry 4.0 technologies and traditional production teams presents both a challenge and an opportunity for UK food manufacturers. By taking decisive action to upskill existing employees, restructure teams, and attract new talent, companies can not only address current skills shortages but position themselves for long-term competitive advantage.
The food manufacturers that will thrive in the coming decade will be those that recognise that their people strategy is as important as their technology strategy. Advanced automation, robotics, and data analytics can transform efficiency and quality—but only when paired with a workforce that has the skills to leverage these technologies effectively.
By investing in their people alongside their technology, food manufacturers can ensure they remain at the forefront of innovation, productivity, and growth in an increasingly competitive global market.
_______________________________________________________________________________________________________________________________________________
Looking to transform your food manufacturing workforce for the Industry 4.0 era? Contact Recruit Mint today to discuss how our specialist recruitment and training services can help you build the right team with the right skills. Visit www.recruitmint.com or call us on 01733 802300.

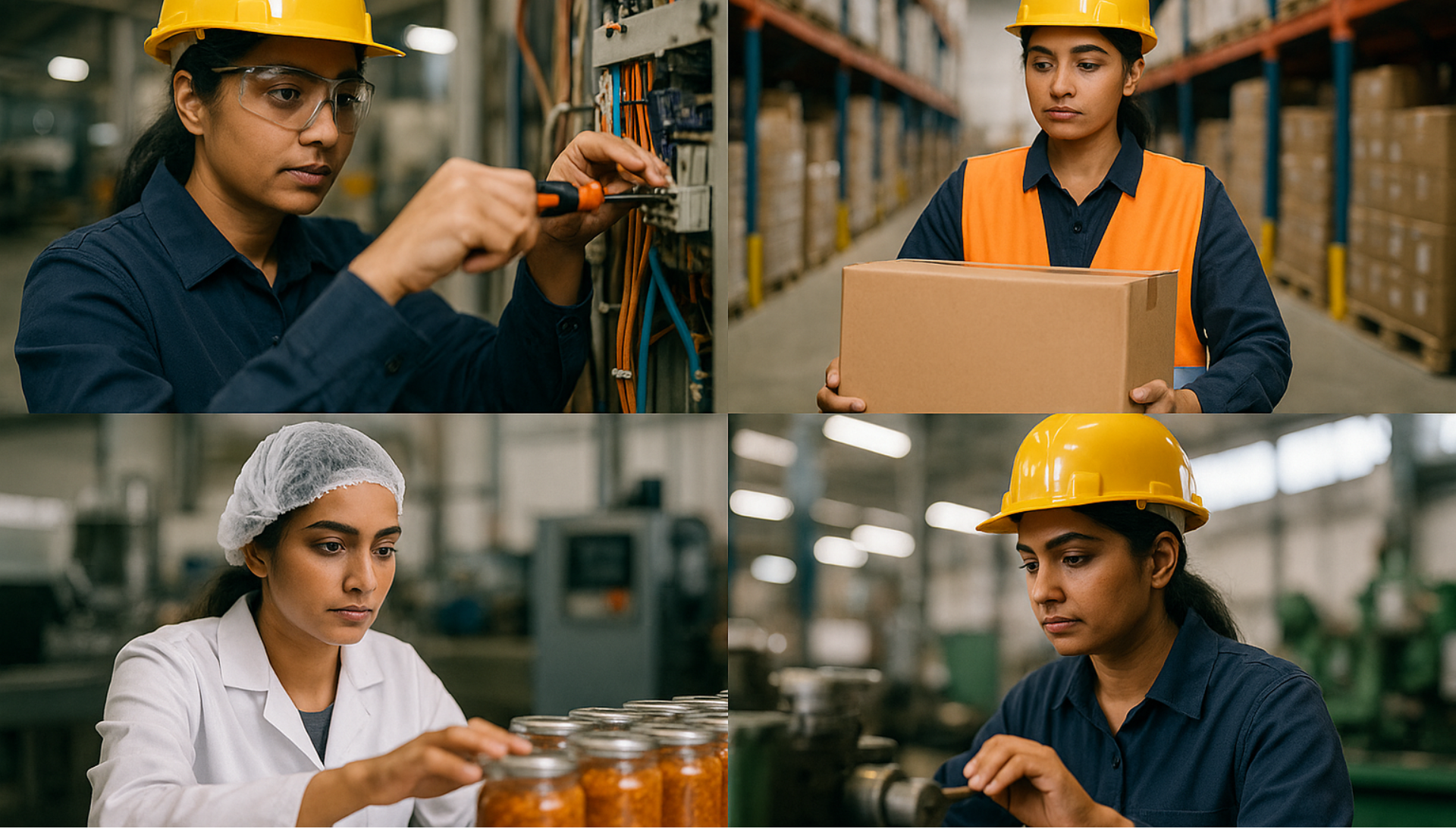
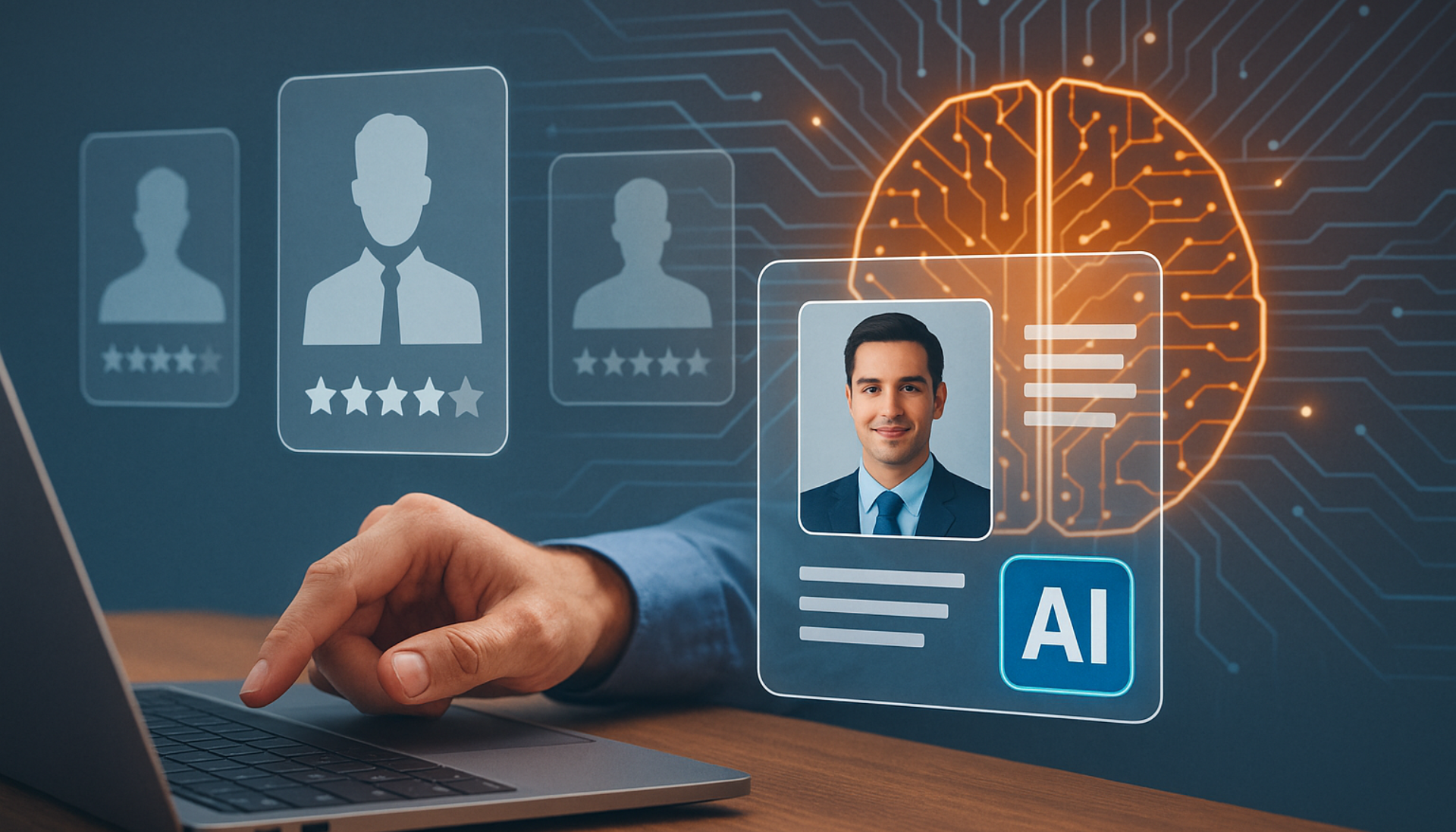
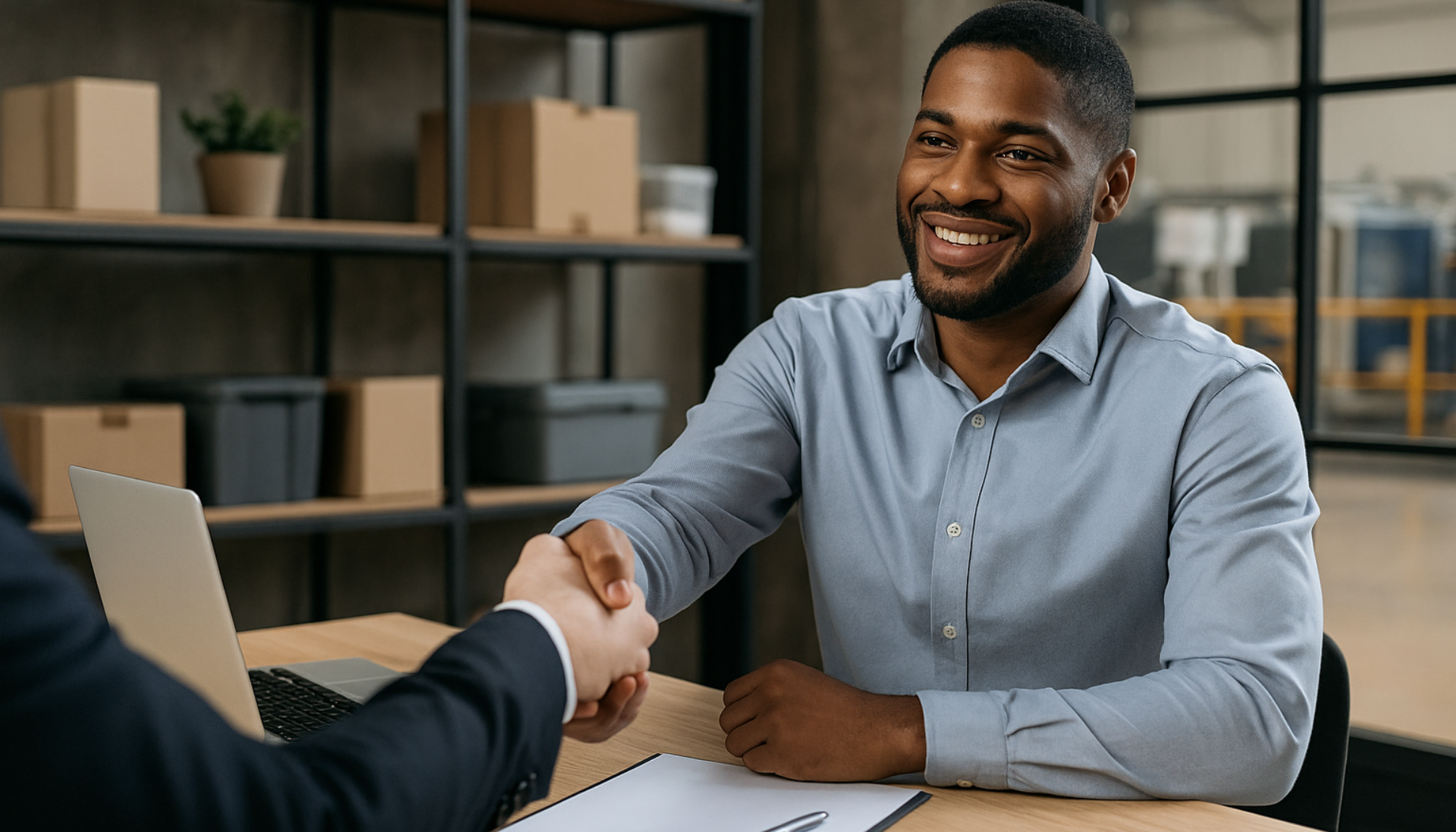
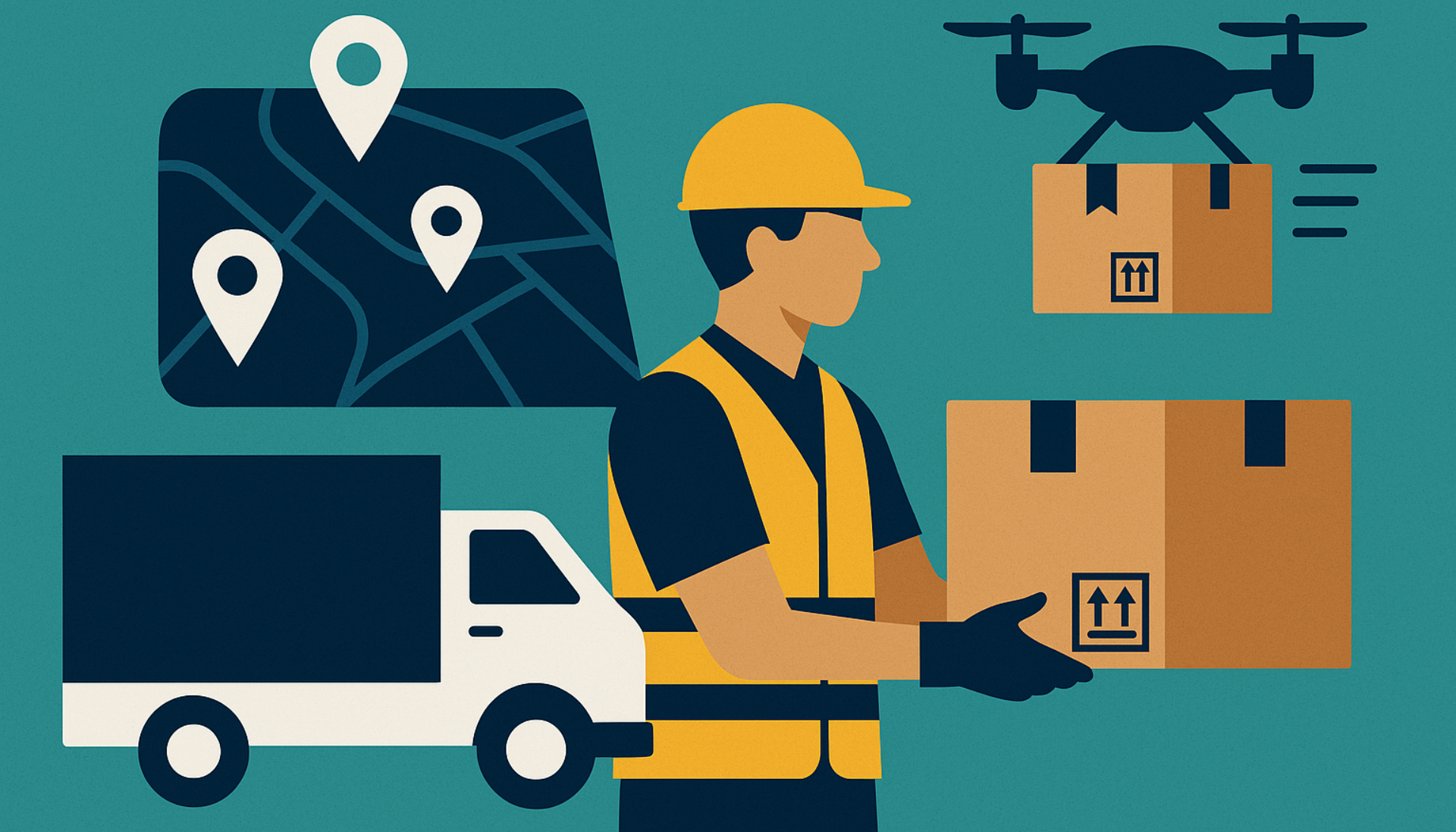
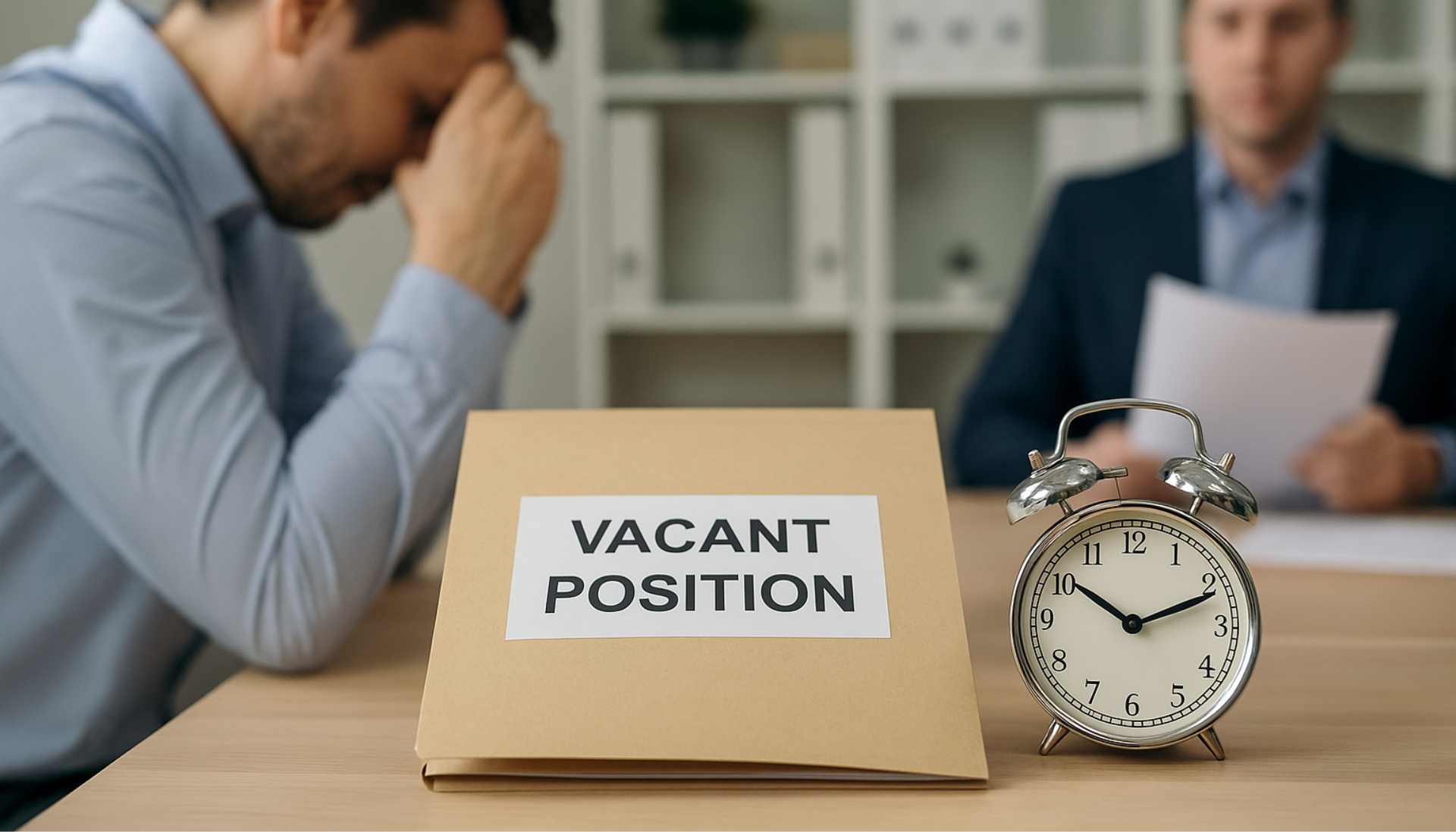
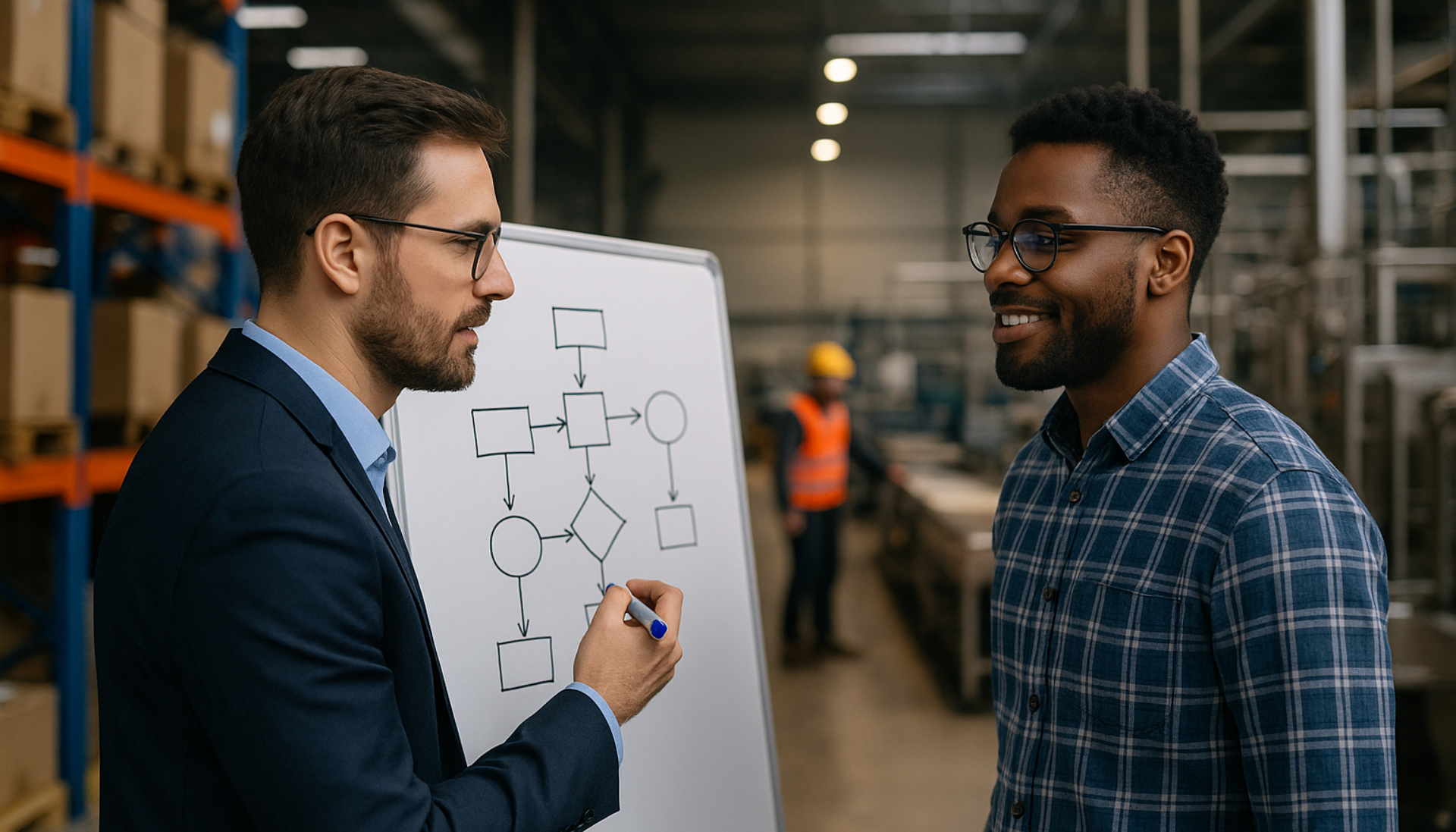
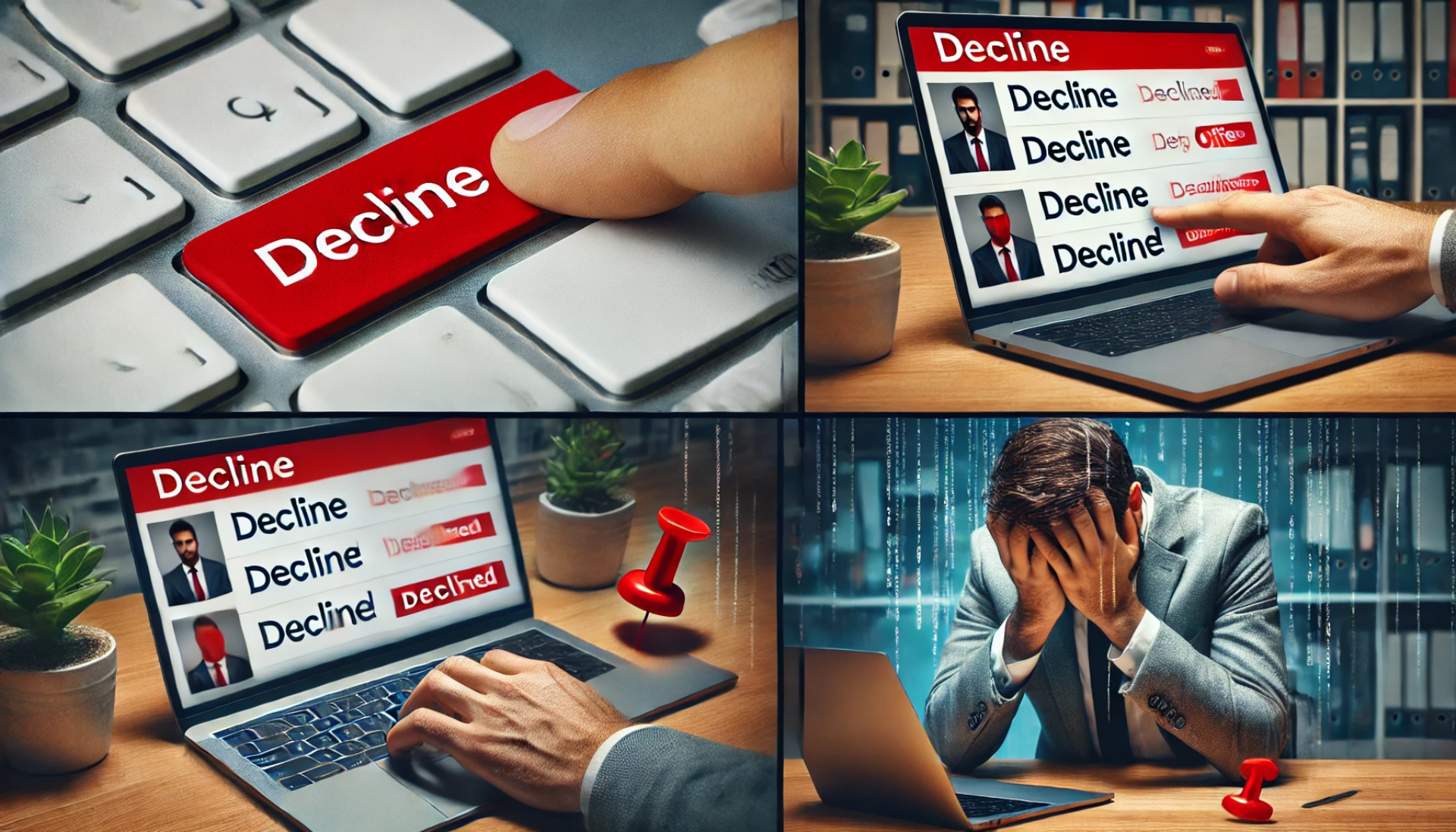
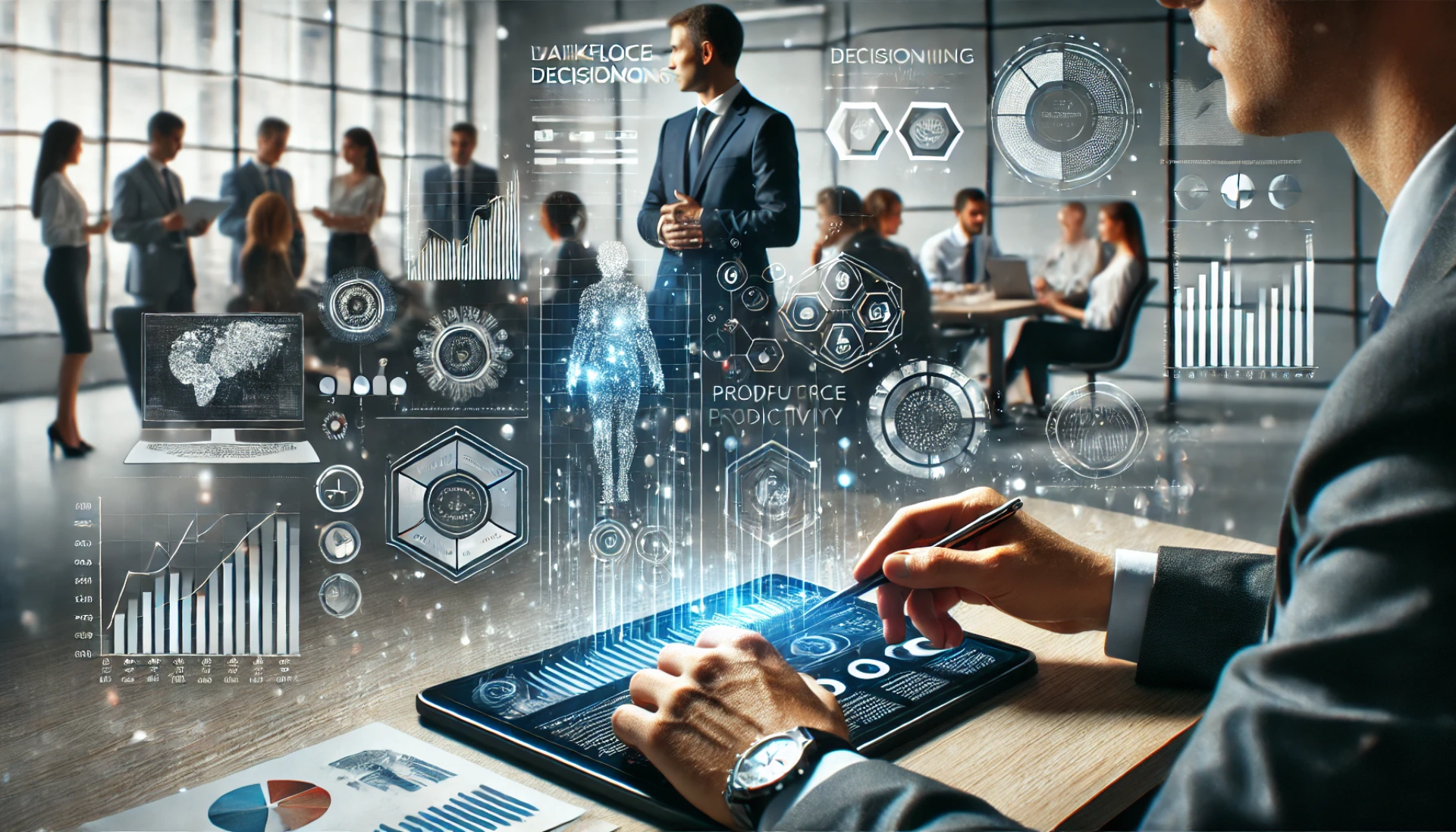
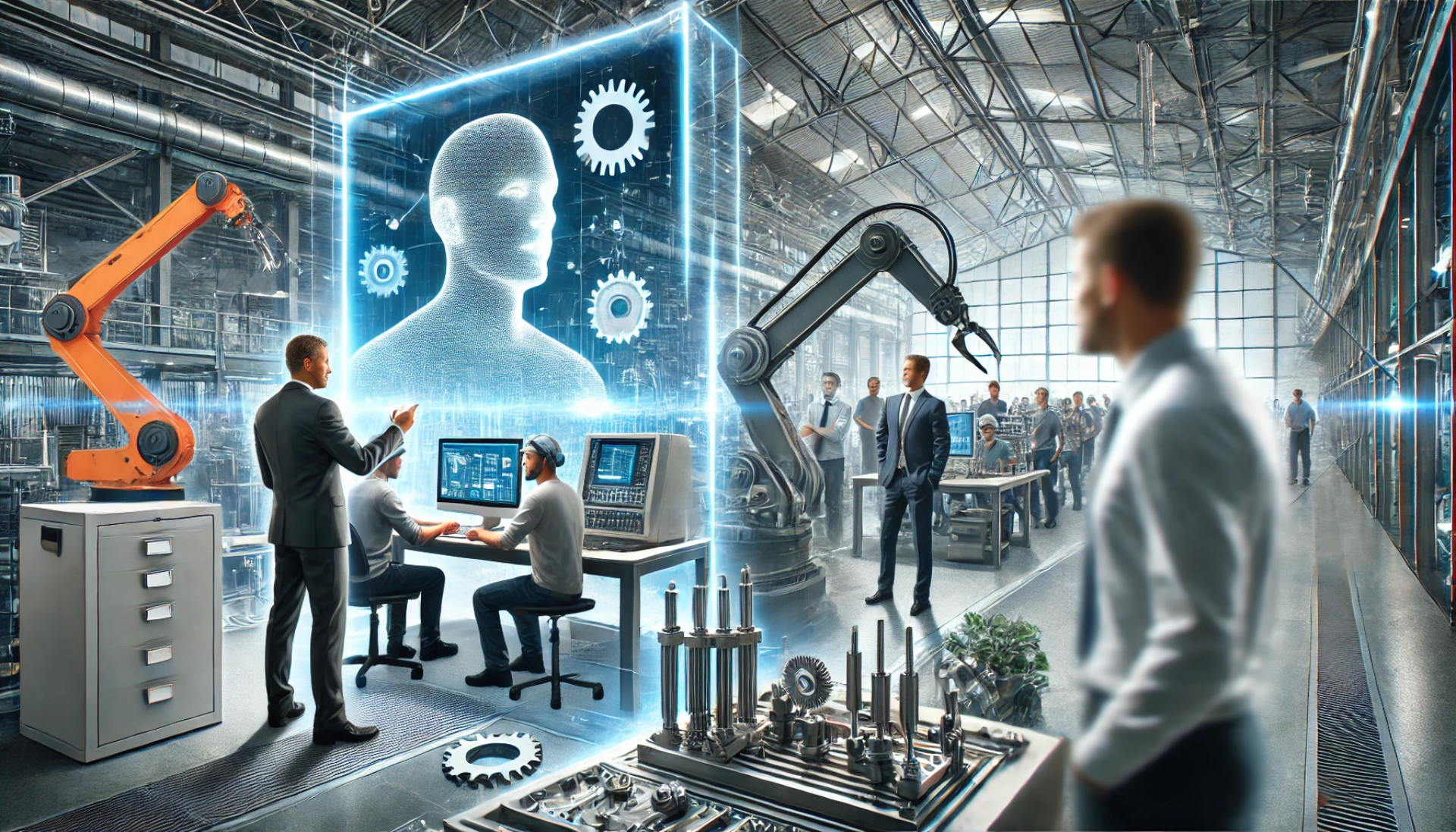